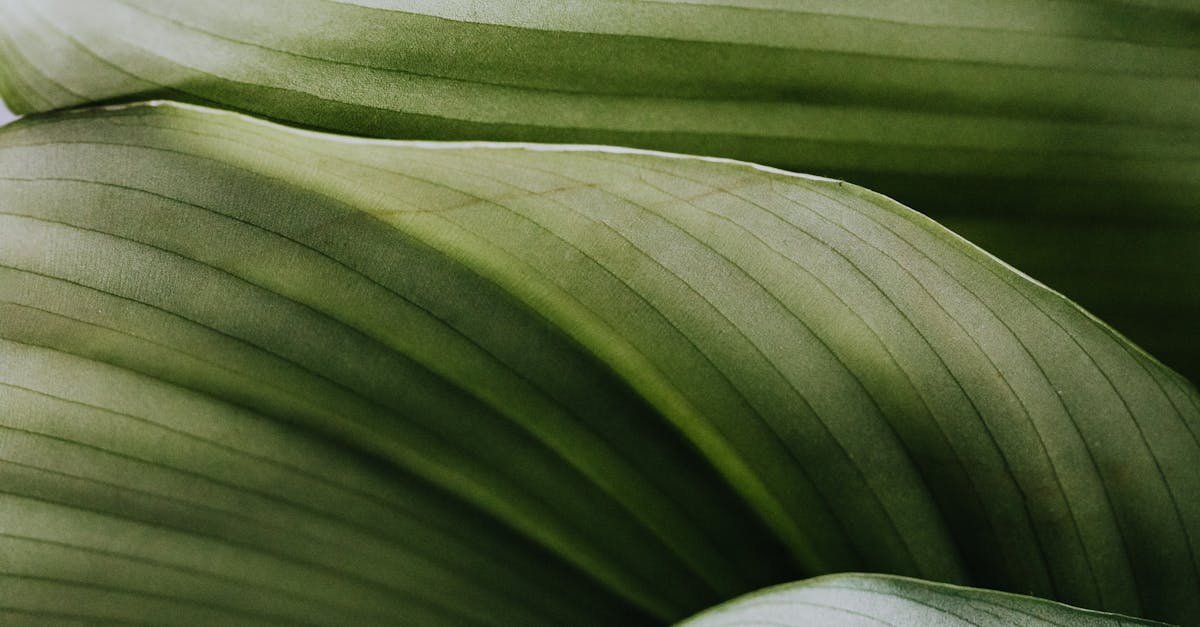
Table Of Contents
PVC and CPVC Pipes
PVC and CPVC pipes are commonly used in various plumbing applications due to their resistance to corrosion and affordability. However, their use in gas line installation and repair is generally discouraged. Natural gas is flammable, and these materials may not meet the stringent safety standards required for gas transportation.
For gas line installation and repair, more suitable materials include steel or polyethylene that have been specifically designed to handle the pressures and risks associated with natural gas. While PVC and CPVC can be suitable for water supply, the unique properties and demands of gas delivery systems make it crucial to adhere to regulations that recommend more robust alternatives.
Considerations for Using PVC in Natural Gas
When considering the use of PVC for natural gas applications, it is vital to acknowledge its limitations. PVC pipes are known for their resistance to corrosion and affordability, but they are not suitable for transporting natural gas. The material lacks the necessary strength and flexibility to withstand the high pressure associated with gas transmission. Additionally, PVC can become brittle over time, particularly when exposed to sunlight and extreme temperatures. This degradation poses significant risks and can lead to potential failures in the gas line.
For gas line installation and repair, industry standards typically favour materials specifically designed for high-pressure applications. Alternatives such as steel or polyethylene are preferred due to their mechanical strength and overall durability. These materials are better equipped to handle the environmental factors and stresses introduced during gas transportation. Adhering to these guidelines ensures a safer and more reliable pipeline system capable of meeting regulatory requirements.
Welded vs. Seamless Pipes
When it comes to gas line installation and repair, selecting the right type of pipe is crucial. Welded pipes are produced by joining metal pieces. This method allows for the creation of longer lengths, which can reduce the number of joints and potential leak points in a gas line. Welded pipes can often handle higher pressures, making them a preferred choice for many natural gas applications.
Seamless pipes, on the other hand, are created from solid round steel and have no welding seams, offering improved structural integrity. This seamless design makes them highly resistant to pressure and stress, which can be essential for ensuring safety in gas line installation and repair. While seamless pipes tend to be more expensive, the benefits they provide in specific applications can justify the higher cost. Both types of pipes have their pros and cons, leading to varied suitability depending on the project requirements.
Comparing Pipe Integrity and Performance
The integrity of pipes used in natural gas applications significantly affects the performance of gas line installation and repair. Pipes must be resilient against both external pressures and the corrosive nature of gas. Materials such as steel, particularly carbon steel, are often preferred due to their strength and ability to withstand harsh environmental conditions. The choice between welded and seamless pipes is crucial, as seamless pipes generally offer better resistance to pressure and reduced risk of leakage, thus enhancing both safety and longevity.
Performance in terms of pressure management is another critical aspect. Pipes need to maintain their structural integrity under high pressures often associated with gas lines. Regular inspections and adherence to installation standards become essential to ensure that any potential weaknesses are identified and addressed promptly. This attention to detail during gas line installation and repair can prevent failure and mitigate risks to safety, highlighting the importance of quality materials and construction techniques.
Installation Standards
Proper installation of natural gas pipelines is crucial for ensuring safety and efficiency. The standards set by relevant regulatory bodies dictate various aspects of gas line installation and repair, including material selection, pressure testing, and routing. It is essential that qualified professionals carry out these installations to comply with the Australian standards for gas installation, as improper techniques can result in hazardous leaks or system failures.
In addition to adhering to material specifications, the installation process must also include thorough inspections at different phases. These inspections help identify potential issues early in the process and ensure that all components meet stringent safety criteria. Regular maintenance and checks are equally important, reinforcing the integrity of the gas line over time and ensuring that it continues to function correctly within the established guidelines.
Regulatory Guidelines for Natural Gas Pipelines
Regulatory guidelines for natural gas pipelines are crucial in ensuring safety and reliability. These guidelines dictate the materials used, installation practices, and maintenance protocols that must be followed. Authorities such as the Australian Energy Regulator oversee compliance with these regulations, which are designed to minimise risks associated with natural gas transport. Adhering to these standards is essential for preventing hazardous incidents and ensuring public safety.
Gas line installation and repair must be performed by licensed professionals familiar with local regulations. Various codes, such as the AS/NZS 5601 series, provide a framework for safe practices, covering aspects from design to operational procedures. Routine inspections and proper record-keeping are also mandated to maintain pipeline integrity and address any issues before they escalate. Compliance with these guidelines is vital for the ongoing safe operation of natural gas infrastructure.
FAQS
What types of pipes are commonly used for natural gas lines?
The most commonly used pipes for natural gas lines are steel, particularly welded and seamless pipes, as well as polyethylene (PE) pipes. PVC and CPVC are generally not recommended for gas applications due to their limitations.
Why are PVC and CPVC pipes not suitable for natural gas?
PVC and CPVC pipes are not suitable for natural gas because they can become brittle over time, especially when exposed to UV light or extreme temperatures. This brittleness can lead to cracks or failures in the pipeline.
What is the difference between welded and seamless pipes for natural gas lines?
Welded pipes are made by joining together flat strips of steel, while seamless pipes are manufactured from a single piece of steel, which reduces the risk of leaks and improves overall integrity. Seamless pipes are often preferred for high-pressure applications.
What installation standards must be followed for natural gas pipelines?
Natural gas pipeline installations must adhere to strict regulatory guidelines that include proper material selection, installation techniques, pressure testing, and maintenance protocols to ensure safety and compliance with local laws.
Are there any special considerations for installing natural gas pipes?
Yes, special considerations include ensuring proper ventilation, avoiding sharp bends in the piping, using appropriate fittings and connections, and following local regulations and safety standards to prevent leaks and ensure safe operation.