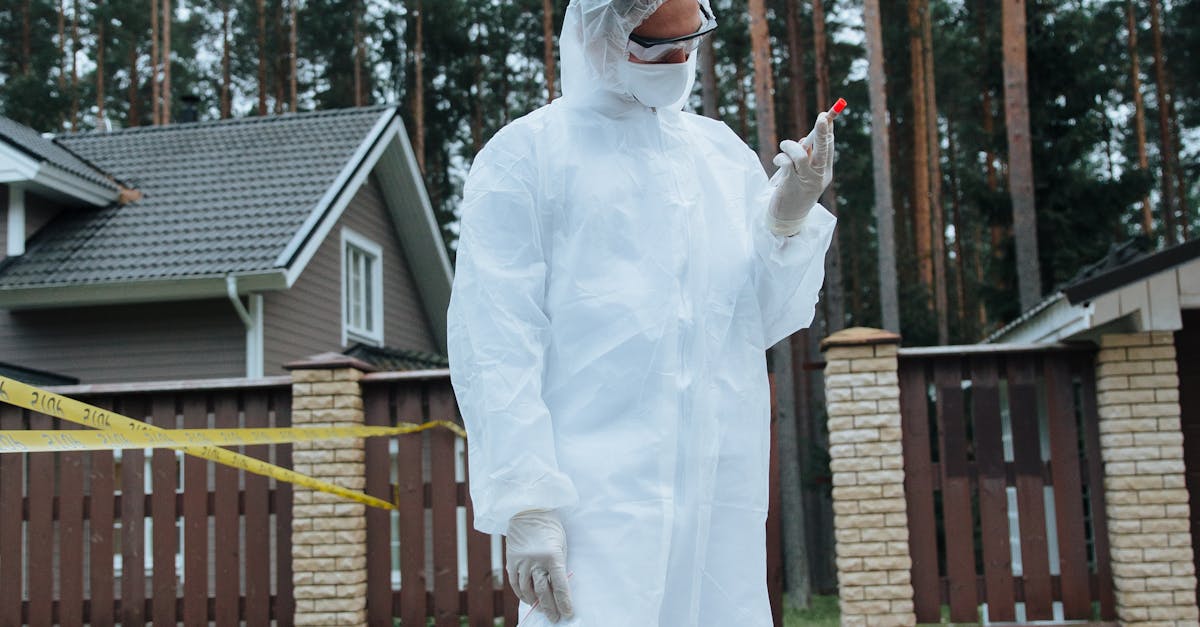
Table Of Contents
Case Studies
In a recent case study involving a large municipal water utility in Australia, the significant costs associated with leakage were highlighted. The utility reported that over a five-year period, unaddressed leaks resulted in millions of dollars in lost revenue. By implementing a comprehensive leak detection and repair strategy, the utility was able to identify and rectify problematic areas within its ageing infrastructure. This proactive approach not only reduced water wastage but also improved overall system efficiency, leading to enhanced financial performance.
Another example can be seen in the industrial sector, where a manufacturing plant experienced substantial operational losses due to undetected leaks in its pipeline system. The facility analysed its water usage and discovered that a systematic leak detection and repair programme could save the business thousands of dollars annually. By investing in advanced monitoring technologies and regular maintenance checks, the plant manager witnessed a marked decrease in both water expenditure and repair costs, ultimately contributing to a stronger bottom line.
RealWorld Examples and Their Financial Impact
Industries across various sectors have faced significant financial repercussions due to leakage issues. For instance, a manufacturing facility in New South Wales reported losses exceeding AUD 200,000 annually as a direct result of unaddressed water leaks. This situation not only increased operational expenses but also necessitated costly repairs and maintenance. Incorporating a robust leak detection and repair programme helped the facility reduce these losses by promptly identifying and addressing leaks before they escalated into larger problems.
Another compelling example can be found in the agricultural sector, where a Queensland farm experienced a steep decline in crop yield due to water system leaks. The fiscal impact extended beyond immediate water costs, affecting overall productivity and profitability. By investing in advanced leak detection and repair technologies, the farm was able to significantly minimise its water wastage and enhance its resource management. The initial investment paid off rapidly, leading to substantial long-term savings and improved crop reliability.
Tools and Techniques for Measuring Leakage
Measuring leakage effectively requires a combination of advanced tools and established techniques. Acoustic sensors are frequently used to detect leaks in water pipes by picking up the sound of water escaping under pressure. Infrared thermography can also play a crucial role in identifying leaks, particularly in insulation or hot water systems. Each method offers unique advantages depending on the specific environment and type of system in place.
Regular monitoring and maintenance are essential for effective leak detection and repair. Implementing a scheduling system for routine inspections can highlight potential issues before they become significant problems. Moreover, combining real-time data analysis with advanced imaging technologies can enhance the effectiveness of leak detection efforts. By prioritising these tools and techniques, organisations can reduce the financial impact of leakage, ultimately leading to more efficient operations.
Effective Methods for Detection
Various methods are available for effective leak detection and repair. One widely used approach is pressure testing, which involves checking the integrity of a system by measuring its pressure levels. This technique helps identify weak points where leaks may occur, providing a clear opportunity for addressing potential issues before they escalate. Acoustic monitoring is another effective method, utilising sound waves to detect leaks in pipes. This non-invasive technique can pinpoint the exact location of a leak, allowing for precise repairs.
Visual inspections also play a crucial role in leak detection and repair. Regular and thorough inspections can uncover signs of leakage, such as water stains, damp patches, or corrosion. Additionally, modern technology has brought about the use of thermal imaging cameras, which detect temperature variations that may indicate hidden leaks. By integrating these methods into routine maintenance schedules, businesses can proactively identify leaks, minimise water loss, and ultimately reduce the financial impact associated with leakage.
Strategies for Reducing Leakage Costs
Reducing leakage costs requires a proactive approach that begins with understanding the sources of leakage within a system. Regular inspections and thorough assessments can help identify weak points where leaks are more likely to occur. Incorporating technologies such as remote monitoring systems can increase the effectiveness of these inspections, enabling teams to detect leaks early and minimise water loss. This systematic approach is crucial for companies looking to manage operational expenses effectively.
Leak detection and repair strategies should be integrated into daily operations to ensure sustainability. Training staff on the importance of monitoring and maintaining equipment can further enhance the effectiveness of these strategies. Implementing scheduled maintenance checks and using advanced leak detection tools will facilitate quick repairs, thus reducing the overall financial impact. A cohesive effort in this area can lead to significant savings while promoting efficient resource utilisation.
Implementing Best Practices in Your Operations
Implementing best practices in operations is essential for minimising leakage costs. Regular audits and monitoring can help identify potential problem areas before they escalate into significant issues. This proactive approach allows businesses to allocate resources effectively and maintain operational efficiency. Establishing clear guidelines for maintenance can also encourage teams to report leaks promptly, ensuring timely action is taken.
Adopting advanced technologies plays a critical role in enhancing leak detection and repair efforts. Utilising sensors, data analytics, and remote monitoring tools enables organisations to detect leaks early, greatly reducing the financial impact. Training staff to recognise signs of leakage fosters a culture of awareness and responsibility. By integrating these best practices into standard operating procedures, companies can experience sustained reductions in leakage costs, ultimately boosting their bottom line.
FAQS
What is leakage and why is it important to measure its cost?
Leakage refers to the loss of resources, such as water or energy, due to inefficiencies or faults in a system. Measuring its cost is crucial as it helps identify areas for improvement, reduce waste, and save money.
How can leakage impact my business financially?
Leakage can lead to significant financial losses due to increased operational costs, wasted resources, and damage to equipment. Addressing leakage can enhance efficiency and improve overall profitability.
What tools are available for measuring leakage?
Various tools exist for measuring leakage, including flow meters, thermal imaging cameras, and acoustic sensors. These tools help detect leaks and assess their impact on operations.
What are some effective methods for detecting leakage?
Effective methods for detecting leakage include regular inspections, pressure testing, and using advanced technologies like infrared thermography or ultrasonic testing to locate leaks accurately.
What best practices can I implement to reduce leakage costs?
Best practices for reducing leakage costs include regular maintenance of equipment, employee training on leak detection, analysing data for patterns, and investing in modern technologies that enhance system integrity.